QM Manual
Create a QM manual according to ISO 9001 or ISO 13485 correctly

Create a QM manual correctly
If you would like to create a QM manual according to ISO 9001 or ISO 13485 correctly for the first time, you will receive advice and support from our QM team. They then have much less effort than expected. Our QM team specialises in industrial software and medical software.
A QM manual, whether based on ISO 9001 or ISO 13485, serves as the foundation of quality management. The ISO 9001 standard applies to manufacturing companies and service providers across all industries, while ISO 13485 is specific to medical device manufacturers.
Is a QM manual mandatory?
Is it mandatory to create a QM manual?
First, the question arises as to whether it is mandatory to create a QM manual. Although ISO 9001 no longer requires the creation of a QM manual since 2015, the manual makes it easier for employees, auditors and customers to get started with their company's quality management. The updated ISO 13485 (2016) still explicitly requires a QM manual.
However, this does not have to be a paper version of a QM manual according to ISO 13485, but an electronic version, e.g. in an internal company intranet, is also permitted. This also applies to the QM manual according to ISO 9001.
At SINOVO, we support companies that produce industrial software or medical devices in creating effective QM manuals.
Support for your QM manual according to ISO 9001 or ISO 13485
If you would like to set up a QM manual according to ISO 9001 or ISO 13485 or adapt an existing one, our QM team will be happy to provide you with support and advice.
Initial Development and Formulation
Support in setting up and formulating a QM manual if you are planning to introduce a quality management system and have it certified:
- Advice and support in the preparation of quality management documentation, adapted to the company-specific company processes.
- Creation of the structure for the QM manual including cover sheet, table of contents, procedural instructions. This also includes decisions on the contents of the QM manual, i.e. procedural instructions, work instructions and forms and the provision of corresponding templates.
- Determination of documentation standards, such as software or standards for corporate design.
- Description of the processes used to provide the services and manufacture the products. Determination of which specific requirements of specific norms and standards have an impact on the individual processes of the respective areas. Determination of regulations from standards that can be excluded.
- Support in the final editing of the texts, final review and approval of the QM manual.
Gap analysis of an existing QM manual
If your company already has a quality management system, we can perform a gap analysis on your existing QM manual to identify any missing elements and ensure compliance with relevant standards. This analysis clarifies any additional requirements and necessary actions to bring your QM system up to standard.
What is the content of a QM manual and what is its structure?
Content and structure for a QM manual
Ideally, the structure for a QM manual should be hierarchical and have a specific content. After the cover page in the first place, see in second place, as an introduction, the description of the quality management system. In third place are your procedural instructions of the processes. Work instructions follow in fourth place.
The QM manual should be designed to be as reader friendly as possible. This can be achieved, for example, with concise texts and uniform terminology. The use of graphical tools for visualization, such as flowcharts, also simplifies readability.
The recommended content structure includes:
- Company logo, company name, address and contact details
- Version information
- Author's name
- Purpose of the QM handbook: Introduction to the quality management system and quality management documentation
- Scope of application: for which companies, products or services
- Responsibility and declaration of commitment: the top management declares in writing that it accepts and prescribes all measures listed in the QM manual as binding for the company
- Applicable standards, directives, and legal requirements
- Standards exclusions (if any)
- Overview of company organization (without specific names)
- Structure topics according to their relevance in daily operations
- Number and mark chapters to indicate any changes or additions
- Leadership and management processes: e.g. description of the quality policy, the corporate guidelines, the target agreements and plans, the documentation for the exchange of information
- Supporting management processes: e.g. documentation of internal audits and management evaluation, description of document management including documentation of the quality management system or supplier evaluations
- Service delivery processes: these are core processes, such as the development of products or services
- Monitoring processes
- Testing and optimization processes: e.g. handling corrective/improvement measures, description of preventive measures
Each process description includes:
- the description of the purpose
- the division into process steps
- the description of the influencing factors
- Input and output
- Main responsible person
- Reference to related documents
- Detailed guidance on performing specific tasks as outlined in the process instructions
- Forms: required by process instructions and serve as records for specific process steps
- Templates: used for creating standardized documents, such as technical documentation
- Glossary of abbreviations and terms to assist readers
- Relevant documents
- Exemplary documents and records of individual processes
DO YOU NEED SUPPORT WITH THE CREATION OF YOUR QM MANUAL?
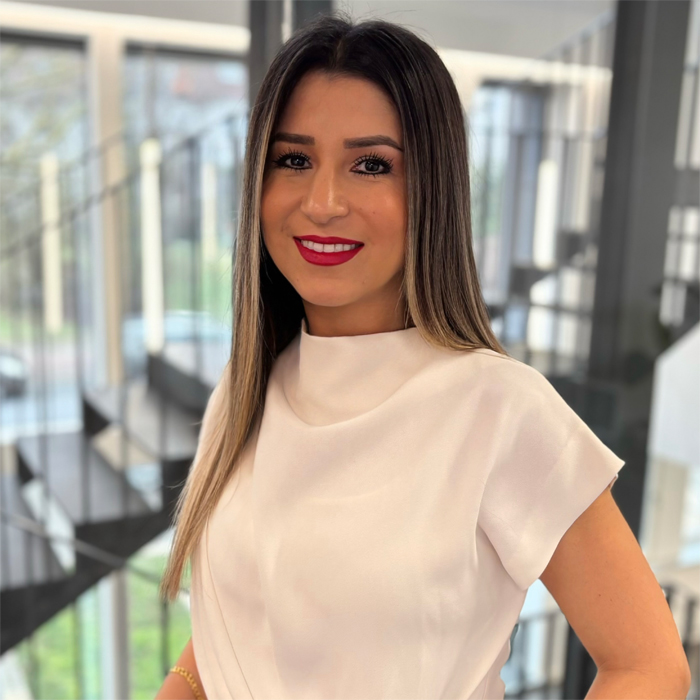
